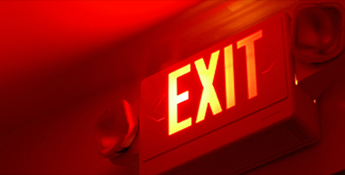
Our factory-trained technicians insure your facility's emergency lighting and exit lights will operate as designed in the event of an emergency. Be sure you are fire-code compliant.
Our preventative maintenance plans provide inspection of your equipment to identify and correct potential problems before a crisis occurs. Our comprehensive plans additionally provide all-inclusive coverage for any emergency or failure, with the peace of mind that an authorized factory-trained technician will be on site to address your problem within a matter of hours.
See our Product Page for a sampling of our extensive new and replacement parts available.
Factory Authorized Emergency Lighting & Code Compliance Program Specifications:
Performed by our technicians at your facility:
- Test all batteries, chargers, and lamps.
- Re-calibrate chargers where needed (both float and high-charge rates) in order to prolong battery life.
- Tighten and adjust any loose emergency lighting fixtures to direct toward points of egress.
- Clean battery terminals of corrosion and coat with protective spray.
- Check electrolyte levels in batteries and refill, if necessary.
- Place dated inspection ticket, noting work performed, on each emergency lighting unit where doing so will not detract from the aesthetics of the area.
- All gel-type batteries will be cycled in order to eliminate memory effect.
- After each semi-annual inspection and service, a detailed and signed report shall be forwarded to you detailing any repairs completed in compliance with N.F.P.A. 101 Sec. 31-1 requirements.
- Upon your approval, any parts installed or replaced will be warranted (parts and labor) 100% for three full years.
- During the six months between the semi-annual maintenance visits, we will respond at no charge for labor or travel in order to correct deficiencies.
- Should any batteries need to be disposed of, they will be done in compliance with current E.P.A. recycling requirements.